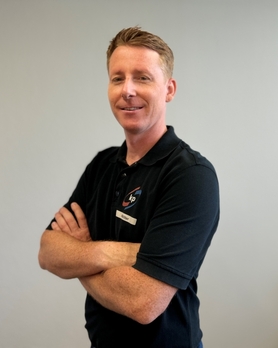
For kp, the project was led by Cell Manager Extrusion, Michael Witter. For Michael and the global kp team, the project was about more than just reducing downtime. It was about improving safety, refining overall efficiency and freeing up valuable operator time to focus on higher-value tasks for our customers.
An additional benefit of the new machine is that reducing stops and disruptions makes more efficient use of energy and resources, and reducing the risk of human error in extrusion roller cleaning lessens the potential for waste, aligning with our ‘Investing in Better’ sustainability strategy and our ethos of ‘Packaging with Integrity’ to create sustainability-focused packaging that everyone can feel good about. And that doesn’t just mean in terms of materials and circularity, it can also be process-driven. As Michael describes it, the approach is about ‘building the new’ rather than ‘fighting the old’.
Sometimes, to move our industry forward, we need to challenge convention and rethink traditional methods.